H2Giga
Die H2Giga-Projekte im Detail
Welche H2Giga-Projekte gibt es? Woran forschen sie genau? Auf dieser Seite finden Sie Informationen zu den 30 Projekten von H2Giga unterteilt in Scale-up-, Next-Generation-Scale-up- und Innovationspool-Projekte sowie ein übergreifendes Plattform-Projekt.
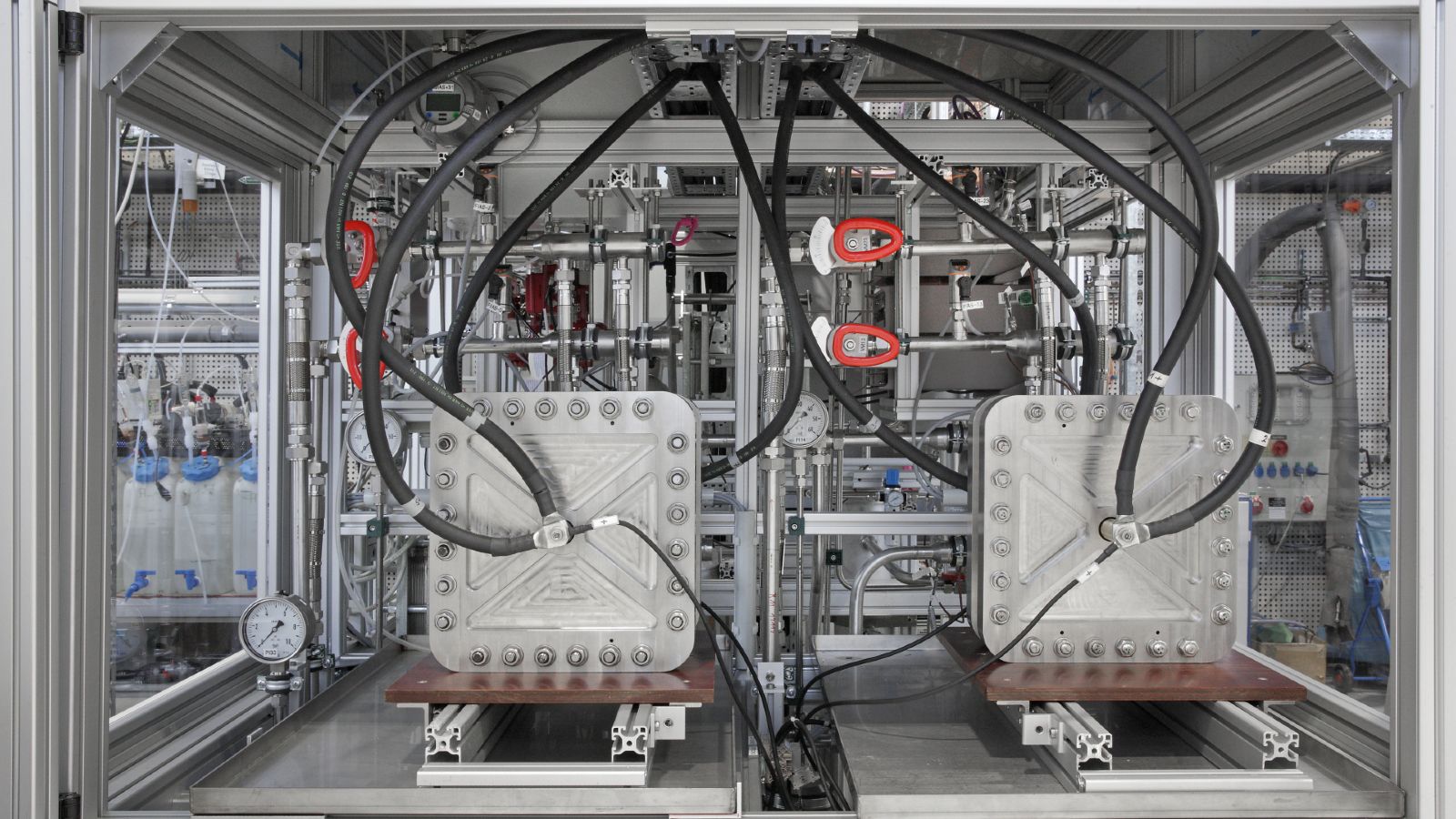
Die H2Giga-Projekte sind in drei Gruppen aufgeteilt: die Scale-up-Projekte, die Next-Generation-Scale-up-Projekte und die Innovationspool-Projekte. Zudem gibt es ein übergreifendes Plattform-Projekt.
Technologien für die Serienfertigung zu den Scale-up-Projekten
Neueste Verfahren werden hochskaliert zu den Next-Generation-Scale-up-Projekten
Wissenslücken schließen zu den Innovationspool-Projekten
Technologieplattform Elektrolyse zum Plattform-Projekt
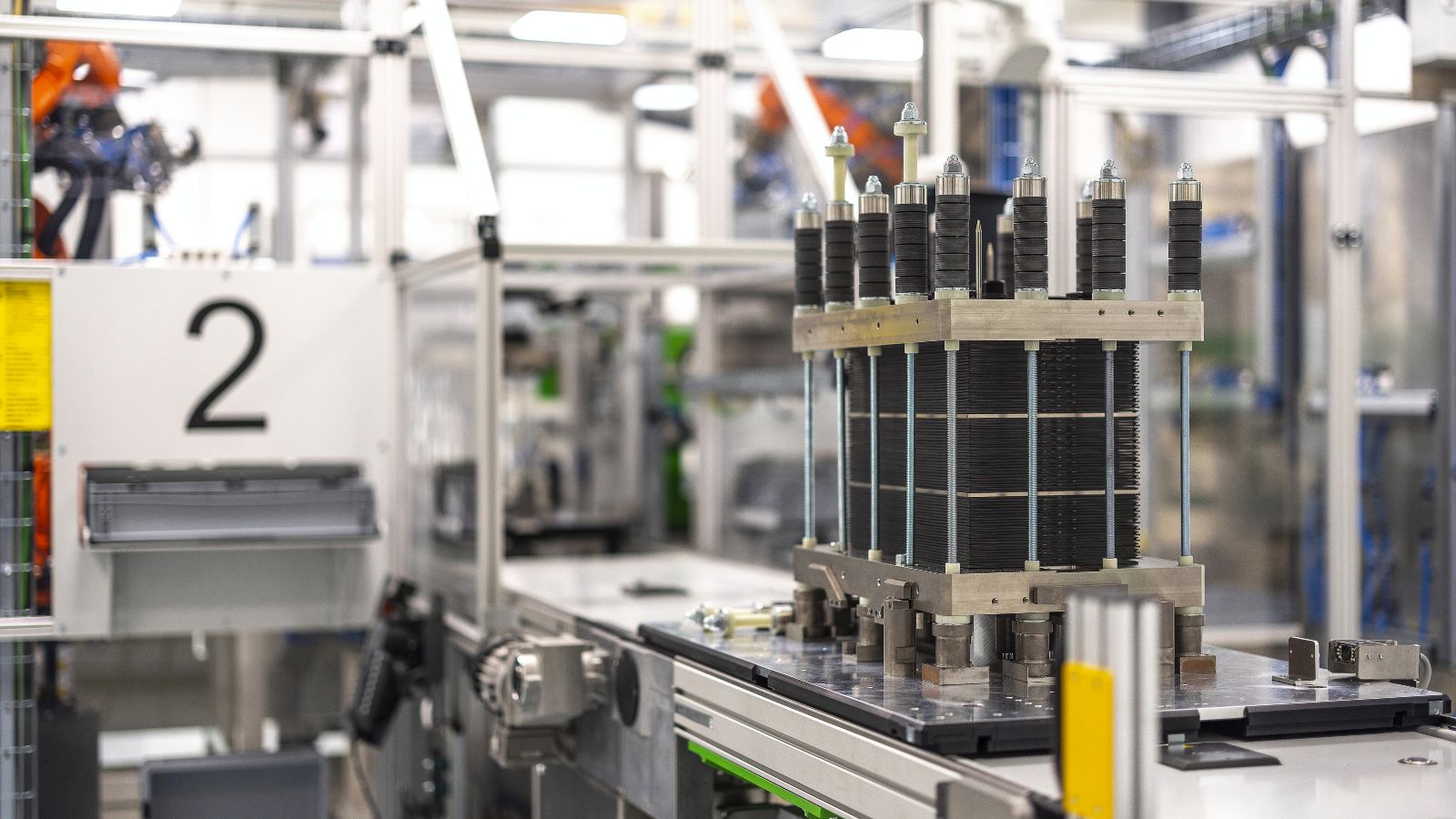
Scale-up-Projekte: Technologien für die Serienfertigung
H2Giga umfasst zahlreiche Projekte zum Thema Scale-up. Darin wollen Elektrolyseurhersteller etablierte Elektrolyse-Verfahren bereit fürs Fließband machen (PEM-Elektrolyse, alkalische Wasserelektrolyse, Hochtemperatur-Elektrolyse). Heute ist die Herstellung von Elektrolyseuren meist Handarbeit. Die Scale-up-Projekte wollen das ändern. Die Herausforderungen reichen dabei von den verwendeten Materialien über die Hochskalierung bis zu Technologien für die Fertigung der Elektrolyseure. An diesen Fragestellungen arbeiten Industrie und Forschung gemeinsam, um eine automatisierte Fertigung von Elektrolyseuren im Gigawatt-Maßstab zu realisieren.
SEGIWA erforscht automatisierte Fertigungsmethoden für PEM-Elektrolyseure, um Produktionskapazitäten im Gigawatt-Bereich zu erreichen. Es umfasst alle Fertigungsschritte von Einzelkomponenten bis hin zu kompletten Stacks.
Im Projekt SEGIWA geht es darum, die Herstellung von speziellen Geräten zur Wasserstoffproduktion, sogenannten PEM-Elektrolyseuren, in hohen Volumina auszubauen. Denn um zukünftig Grünen Wasserstoff in der erforderlichen Menge herstellen zu können, müssen für die Herstellung der Elektrolyseure Produktionskapazitäten im Gigawatt-Bereich aufgebaut werden.
Die Partner im Projekt entwickeln hierzu Technologien zur automatisierten Fertigung und realisieren diese. Sie untersuchen, wie Materialien und Recycling-Konzepte in einer Serienproduktion am besten zusammenspielen. In der Forschungsphase entwickeln und erproben die Projektbeteiligten technische Details zu einzelnen Produktionsprozessen, deren Verknüpfung im Produktionssystem sowie zu den erforderlichen Ausbaustufen der Fabrikation.
Ein weiterer innovativer Ansatz ist die Nutzung digitaler Zwillinge sowohl in der Fertigung als auch in der installierten Flotte. Diese virtuellen Modelle helfen, die Anlagen im Feld zu analysieren und zu verbessern. Sie ermöglichen eine vorausschauende Planung von Wartungen und einen optimierten Betrieb der Anlagen zur Wasserstofferzeugung.
Langtitel: |
Serienproduktion von Elektrolyseuren im Gigawatt-Bereich |
Förderkennzeichen: |
03HY121A-K |
Gesamtfördersumme: |
ca. 34,8 Mio. Euro |
Partner: |
Siemens Energy Global GmbH & Co. KG, Forschungszentrum Jülich GmbH, RWTH Aachen, Hahn-Schickard-Gesellschaft für angewandte Forschung e. V., Leibniz-Institut für Katalyse e. V., OFFIS e. V., Leibniz Universität Hannover, FUMATECH BWT GmbH, Heraeus Precious Metals GmbH & Co. KG, Main-Automation GmbH, Forschungsinstitut für Rationalisierung e. V. |
Projektlaufzeit: |
01.05.2021 – 31.12.2025 (Teilprojekte enden früher) |
Kontakt in das Projekt: |
Dr. Günter Schmid und Stefan Höyng |
Das Projekt DERIEL untersucht die Alterungsmechanismen verschiedener Elektrolyseurkomponenten. Im Mittelpunkt stehen dabei Untersuchungen möglichst nah am realen Einsatz. Ziel sind geeignete Betriebsstrategien für möglichst langlebige Elektrolyseure.
Die Projektarbeiten erstrecken sich von kleinen Laborzellen bis hin zu Modultestständen mit einer Leistung von 2,5 MW. Dazu haben die Projektbeteiligten einen PEM-Elektrolyse-Teststand für einen Elektrolyseurstack realer Größe im Megawattbereich entwickelt und gebaut. Das Neue dabei: Erstmalig ist ein Elektrolyseurmodul in realer Größe mit Messtechnik ausgestattet, um verschiedene Prozesse im laufenden Betrieb untersuchen zu können. Zu den betrachteten Prozessen zählen Degradations-, Fehler- und Schnittstellen-Mechanismen.
Zur Untersuchung der Alterungsprozesse einzelner Elektrolyseurkomponenten, zum Beispiel Membran-Elektroden-Einheiten, nutzen die Forschenden fortgeschrittene Analysemethoden wie Computertomografie, Elektronenmikroskopie sowie Kernspinresonanz- und Raman-Spektroskopie. Diese Techniken ermöglichen den Vergleich von Materialien vor und nach dem Einsatz im Elektrolyseur. Durch das Verständnis der Vorgänge, wie das Wachstum von Katalysatorpartikeln oder Veränderungen in der Elektrodenstruktur, können die Systeme effizienter gestaltet und optimiert werden.
Digitale Zwillinge, die die Prozesse in einem Modell abbilden, unterstützen die Forschenden bei der Datenanalyse. Sie vergleichen die Berechnungen der digitalen Zwillinge mit den Laborergebnissen. Dadurch erlangen sie ein tiefgreifendes Verständnis der Prozesse und können geeignete Betriebsstrategien ableiten. Das Ziel: möglichst langlebige Elektrolyseure.
Langtitel: |
De-Risking PEM-Elektrolyseur |
Förderkennzeichen: |
03HY122A-I |
Gesamtfördersumme: |
ca. 103,9 Mio. Euro |
Partner: |
Siemens Energy Global GmbH & Co. KG, Heraeus Precious Metals, Forschungszentrum Jülich, RWTH Aachen University, FAU Erlangen-Nürnberg, OFFIS e. V., Leibniz-Universität Hannover, Ruhr-Universität Bochum, MPI-CEC |
Projektlaufzeit: |
01.06.2021 – 31.12.2025 (Teilprojekte enden früher) |
Kontakt in das Projekt: |
Dr. Günter Schmid |
SineWave optimiert die gesamte Elektrolyseanlage und ihre Peripheriekomponenten. Ziel ist es, die Technologie für PEM-Elektrolyseanlagen insgesamt mit Hinblick auf verschiedenste Anwendungen zu optimieren, einschließlich innovativer Materialien und Strategien der Betriebsführung, sowie der Integration in bestehende Produktionsprozesse.
Das Projekt SineWave konzentriert sich darauf, die Effizienz von PEM-Elektrolyseanlagen zu steigern, auch im Hinblick auf deren Peripheriekomponenten. Ziel ist es, eine Technologieplattform zu entwickeln, die unabhängig von der Größe der Anlage nutzbar ist. Hierbei wird besonderes Augenmerk auf maßgeschneiderte Komponenten gelegt, wie beispielsweise Systeme zur Trennung von Sauerstoff und Wasser.
Um die Materialien und Komponenten zu testen, werden spezielle Prüfstände errichtet, an denen die Leistungsfähigkeit und das Verschleißverhalten in sogenannten Short-Stacks analysiert werden. Weiterhin wird das Gesamtsystem daraufhin überprüft, wie gut es sich für die Massenproduktion eignet, und innovative Technologien wie die additive Fertigung kommen zum Einsatz.
Ein weiterer wichtiger Aspekt von SineWave ist die Integration des Elektrolyseurs in bestehende industrielle Prozesse, wie die Herstellung von Methanol oder Ammoniak oder die Kombination mit traditionellen Anlagen zur Dampfreformierung von Methan. Hierfür werden geeignete Schnittstellen vorbereitet.
Zudem entwickelt das Projekt digitale Lösungen, die einen sicheren Betrieb des Elektrolyseurs gewährleisten und die intelligente Steuerung des Gesamtsystems ermöglichen. Diese Maßnahmen sollen dazu beitragen, die Gesamt- und Betriebskosten einer Anlage zu senken.
Langtitel: |
Serienproduktion und Industrialisierung von integrierten & sektorgekoppelten Elektrolysesystemen für Wasser |
Förderkennzeichen: |
03HY123A-F |
Gesamtfördersumme: |
ca. 11,3 Mio Euro |
Partner: |
Linde GmbH, ITM Power Germany GmbH, Technische Universität Dresden, Helmholtz-Zentrum Dresden-Rossendorf e. V., Technische Universität München |
Projektlaufzeit: |
01.06.2021 – 30.09.2025 |
Kontakt in das Projekt: |
Anatoly Davydov |
IntegrH2ate zielt darauf ab, die Wirtschaftlichkeit von Großelektrolyseanlagen durch Kostenreduktion sowohl auf Seite der Investitionskosten (CAPEX) als auch auf Seite der laufenden Kosten (OPEX) zu verbessern.
Die großtechnische Realisierung von Elektrolyseanlagen entspricht derzeit nicht den Erwartungen, hauptsächlich wegen ihrer unzureichenden Wirtschaftlichkeit. Dies führt zu zögerlichen Investitionsentscheidungen. Es besteht daher ein dringender Bedarf, die Betriebs- und Investitionskosten von Groß-Elektrolyseanlagen zu optimieren, um ihre Wirtschaftlichkeit zu verbessern.
Um die Wirtschaftlichkeit weiter zu steigern, sollen im Projekt IntegrH2ate einerseits kostenoptimierte Standardmodule für die drei Elektrolysetechnologien PEM, AEL und SOEC durch intelligente Zusammenführung und Weiterentwicklung von Anlagenkomponenten inklusive der Peripherie der Stacks erarbeitet werden, sowie Konzepte für ein anwendungsbezogenes Design von Großanlagen bis zu 1 GW durch geschickte Kombination solcher Module.
Auf der anderen Seite sollen innovative Konzepte zur effektiven Nutzung der Nebenprodukte Sauerstoff und Wärme erforscht werden. Es sollen neue Verfahren zur Reinigung und Verdichtung des Sauerstoffs untersucht werden, um dessen Nutzbarkeit für potenzielle Abnehmer zu konzipieren.
Die bei der Elektrolyse anfallende Abwärme wird ebenfalls nutzbar gemacht. In einer skalierten Demonstrationsanlage wird die Wärme mittels einer Wärmepumpe auf ein höheres Temperaturniveau gebracht. Dadurch lässt sie sich effizienter am Produktionsort nutzen, beispielsweise in Chemieparks oder Raffinerien, aber auch in ein Fernwärmenetz einspeisen. Zudem werden im Rahmen von IntegrH2ate Konzepte zur Optimierung der Wasserreinigung entwickelt.
Langtitel: |
Kostenoptimierung von Groß-Elektrolyseanlagen inklusive Integration der Nutzung von Nebenprodukten (Sauerstoff, Wärme) in zentralen und dezentralen Anlagen |
Förderkennzeichen: |
03HY127A-B |
Gesamtfördersumme: |
ca. 10,0 Mio. Euro |
Partner: |
Linde GmbH, Fraunhofer-IEG |
Projektlaufzeit: |
01.01.2022 – 31.12.2025 |
Kontakt in das Projekt: |
Anatoly Davydov |
Das PEP.IN-Projekt entwickelt Produktionstechnologien und ‑verfahren für die Massenfertigung von PEM-Elektrolyseuren. Es umfasst die gesamte Wertschöpfungskette von der Herstellung bis hin zur Endmontage.
Das Projekt PEP.IN zielt darauf ab, Elektrolyseure in großen Stückzahlen kostengünstig und wettbewerbsfähig zu produzieren. Hierzu entwickeln die beteiligten Partner innovative Produktionstechnologien und -verfahren, die es bisher noch nicht auf dem Markt gibt. Der Ansatz für die Automatisierung und Hochskalierung der Elektrolyse basiert auf Erkenntnissen bei Brennstoffzellen für den Automobilsektor. Daher spielen Automobilhersteller und Zulieferer eine zentrale Rolle in diesem Projekt.
PEP.IN strebt nach Weiterentwicklungen und Kostenreduktionen in allen Wertschöpfungsstufen der Elektrolyseur-Herstellung. Es werden Produktionsverfahren für Serienfertigung in einer sogenannten Giga-Factory entwickelt. Zudem wird das Design der Elektrolyse-Stacks für die automatisierte Produktion optimiert, was als "Design for Production" bekannt ist.
Parallel dazu wird an einem „Stack of the Future“ geforscht, der als Grundlage für zukünftige Generationen von Elektrolyseuren dienen soll. Auch die aktuelle Generation von Stacks wird durch speziell entwickelte Greiftechniken und Assembling-Robotik automatisiert und reproduzierbar zusammengebaut. Verschiedene Konzepte für die Gestaltung von Montagelinien werden sowohl aus akademischer als auch aus industrieller Perspektive erforscht.
Zur Optimierung der Herstellungsprozesse werden intelligente Überwachungssysteme integriert, die einen optimalen Betrieb der Elektrolyseure über deren gesamte Lebensdauer ermöglichen. Bereits in der Entwicklungsphase wird auch an die spätere Wartung gedacht: Intelligente Systeme sollen zur Langlebigkeit und zur Effizienz der Wartung beitragen.
Schließlich entwickeln die Partner im Projekt PEP.IN auch Logistikkonzepte, um eine qualifizierte und massenfertigungsgerechte Lieferkette sicherzustellen. Das Ziel ist es, mittelfristig eine effiziente und skalierbare Produktion von Elektrolyseuren zu etablieren. Durch die Arbeiten in PEP.IN soll mittelfristig eine Produktion von einem Gigawatt Elektrolysekapazität pro Jahr ermöglicht werden.
Langtitel: |
Industrialisierung PEM-Elektrolyse-Produktion |
Förderkennzeichen: |
03HY120A-I |
Gesamtfördersumme: |
ca. 27,3 Mio. Euro |
Partner: |
MAN Energy Solutions SE, Quest One GmbH, AUDI AG, VAF Gesellschaft für Verkettungsanlagen, Automationseinrichtungen und Fördertechnik mbH, Fraunhofer-Institut für Solare Energiesysteme (ISE), Fraunhofer-Institut für Produktionstechnik und Automatisierung (IPA), Fraunhofer-Institut für Umwelt-, Sicherheits- und Energietechnik UMSICHT, Zentrum für Brennstoffzellen-Technik GmbH, Forschungszentrum Jülich GmbH |
Projektlaufzeit: |
01.05.2021 – 31.12.2025 (Teilprojekte enden früher) |
Kontakt in das Projekt: |
Florian Hajdu |
Dieses Projekt konzentriert sich auf die Weiterentwicklung der Stacktechnologie für die Hochtemperatur-Elektrolyse, um sie für die Massenproduktion und den Einsatz im Gigawatt-Bereich zu optimieren.
Der Hochtemperatur-Elektrolyseur (HTEL) ist eine fortschrittliche Technologie zur Erzeugung von Wasserstoff, die besonders gut für industrielle Anwendungen geeignet ist, wo Wasserdampf und industrielle Abwärme vorhanden sind. Diese Technologie nutzt die vorhandene Wärme, um die Effizienz der Wasserstoffproduktion zu steigern, was bedeutet, dass bei gleichem Stromverbrauch mehr Wasserstoff hergestellt werden kann als mit anderen Methoden.
Das Kernstück des HTEL sind die einzelnen Zellen, die zu einem sogenannten Stack zusammengefügt werden. Das Projekt konzentriert sich darauf, diese Stacktechnologie zu verbessern und für die Großproduktion im Gigawatt-Maßstab vorzubereiten. Die Partner im Projekt arbeiten daran, die Lebensdauer und Effizienz der Stacks zu erhöhen und die Kosten für Materialien zu senken. Ein weiterer Schwerpunkt liegt auf der Entwicklung von Fertigungstechnologien und der Hochskalierung der Produktion.
Durch Innovationen sowohl in der Zelltechnologie als auch in der Stackkonstruktion strebt das Projekt eine verbesserte Leistung und Langzeitstabilität an. Außerdem werden die Stacks für zukünftige automatisierte Fertigungsprozesse optimiert. Mit Entwicklungen wie einem automatisierten Stack-Stapler und der Planung eines effizienten Logistiknetzwerks legt das Projekt den Grundstein für die zukünftige industrielle Serienfertigung der HTEL-Stacks im großen Maßstab.
Langtitel: |
Ready for Gigawatt, Serienfertigung großskaliger HTEL-Stacks |
Förderkennzeichen: |
03HY124A-I |
Gesamtfördersumme: |
ca. 17,5 Mio. Euro |
Partner: |
Sunfire GmbH, Fraunhofer-Institut für Keramische Technologien und Systeme (IKTS), Karlsruher Institut für Technologie, Universität Bayreuth, Deutsches Zentrum für Luft- und Raumfahrt e. V., EIfER Europäisches Institut für Energieforschung EDF-KIT EWIV, KERAFOL Keramische Folien GmbH & Co. KG, HORIBA FuelCon GmbH, XENON Automatisierungstechnik GmbH |
Projektlaufzeit: |
01.05.2021 – 31.12.2025 |
Kontakt in das Projekt: |
Katja Mattner |
In diesem Projekt werden Module für Hochtemperatur-Elektrolyseure (HTEL) entwickelt, die in großer Stückzahl herstellbar sind und eine effiziente Wasserstoffproduktion ermöglichen.
Im Projekt werden unter HTEL-Modulen die Einheiten verstanden, in denen HTEL-Stacks – zusammengesetzt aus einzelnen HTEL-Zellen – mit weiteren essenziellen Komponenten verbunden sind. Diese zusätzlichen Komponenten regeln die Zuführung der Rohstoffe und die Abfuhr der Produkte und umfassen auch das Management von Wärme und elektrischer Leistung. Mehrere Module können zu größeren, skalierbaren Elektrolyseanlagen zusammengeschaltet werden.
Um den schnell wachsenden Markt für Wasserelektrolyseure effizient und wirtschaftlich bedienen zu können, arbeiten die Projektpartner an der Entwicklung neuer Generationen von HTEL-Modulen. Diese sollen in großen Stückzahlen produziert werden können und durch geringere Herstellungskosten im Vergleich zu aktuellen Modellen deutlich wirtschaftlicher sein. Ein Schlüssel dazu ist die Optimierung der Technologie für Skalierbarkeit, wodurch erhebliche Kosteneinsparungen durch Skaleneffekte erreicht werden sollen (Design-to-Cost-Ansatz).
Das Projekt umfasst Forschungs- und Entwicklungsarbeiten an diesen neuen HTEL-Modulen, den zugehörigen Produktionsprozessen und Betriebsstrategien. Diese Bemühungen sollen es ermöglichen, den wachsenden Bedarf an Wasserelektrolyseuren kosteneffektiv zu decken. Besonders dort, wo Wasserdampf verfügbar ist, bieten die neuen Module das Potenzial, Wasserstoff besonders effizient zu produzieren.
Langtitel: |
HTEL-Module – Ready for Gigawatt |
Förderkennzeichen: |
03HY125A-D und G-J |
Gesamtfördersumme: |
ca. 16,5 Mio. Euro |
Partner: |
Sunfire AG, DECHEMA Forschungsinstitut, DBI Gas- und Umwelttechnik GmbH, Technische Universität Bergakademie Freiberg, XENON Automatisierungstechnik GmbH, Kontron AIS GmbH, imk Industrial Intelligence GmbH, SMA Solar Technology AG |
Projektlaufzeit: |
01.10.2021 – 31.12.2025 |
Kontakt in das Projekt: |
Katja Mattner |
AEL4GW stellt sich der Herausforderung, eine neue Generation von Druck-Alkali-Elektrolyseuren zu entwickeln, die effizienter arbeiten und eine großskalige, kosteneffiziente Produktion ermöglichen.
Das Projekt AEL4GW widmet sich der Entwicklung einer neuen Generation von Druck-Alkali-Elektrolyseuren. Diese robuste Technologie, bekannt für ihre Ausgereiftheit, soll für einen Betriebsdruck von 30 bar optimiert werden. Ziel ist es, die Effizienz zu steigern und die Technologie für die großskalige und kosteneffiziente Produktion zu adaptieren.
Um dies zu erreichen, werden im Projekt innovative technologische Lösungen wie leistungsfähige Beschichtungstechniken für Elektroden, automatisierte Herstellungsprozesse für Dichtungen und die Modellierung elektrochemischer Prozesse in den Zellen entwickelt. Diese Ansätze ermöglichen eine Modularisierung des Elektrolyseurs, die für die Produktion im Gigawatt-Maßstab notwendig ist.
Der erste Projektabschnitt fokussiert sich darauf, die bestehende Technologie – bestehend aus Zelle, Stack und System – an die aktuellen Anforderungen anzupassen und eine neue Generation von Druck-Alkali-Elektrolyseuren zu entwickeln. Diese Basis dient dann der Skalierung, einschließlich der Entwicklung entsprechender Fertigungs- und Logistikprozesse. Die neuen Konfigurationen werden validiert und die Prozessentwicklung sowie die Fabrikplanung werden bis in den Gigawatt-Bereich vorangetrieben.
Im zweiten Abschnitt des Projekts werden Multi-Megawatt-Elektrolyseanlagen konzipiert, die durch Verschaltung einzelner Elektrolyseure Anlagen über 100 Megawatt ermöglichen. Dabei werden auch Standortfaktoren berücksichtigt, um effiziente Konzepte für große Anlagen zur Produktion von Grünem Wasserstoff zu entwickeln. Als Ergebnis wird ein zentraler Baustein für die Skalierung der Wasserstoffproduktion und für die Dekarbonisierung wichtiger Industriezweige geschaffen.
Langtitel: |
AEL4GW: Ready for Gigawatt, AEL-Serienfertigung großskaliger Alkalielektrolyseure |
Förderkennzeichen: |
03HY126A-C, E-G und I-J |
Gesamtfördersumme: |
ca. 26,6 Mio. Euro |
Partner: |
Sunfire AG, Fraunhofer-Institut für Fertigungstechnik und Angewandte Materialforschung (IFAM), Fraunhofer-Institut für Fabrikbetrieb und -automatisierung (IFF), Alantum Europe GmbH, HAFF-Dichtungen GmbH, Frenzelit Werke GmbH, Deutsches Zentrum für Luft- und Raumfahrt e. V., imk Industrial Intelligence GmbH |
Projektlaufzeit: |
01.10.2021 – 31.12.2025 |
Kontakt in das Projekt: |
Katja Mattner |
Das Projekt INSTALL AWE fördert die Industrialisierung der alkalischen Wasserelektrolyse durch die Entwicklung neuer Stack- und Zellendesigns und automatisierter Montageprozesse.
Das Verbundvorhaben INSTALL AWE zielt darauf ab, die Industrialisierung der alkalischen Wasserelektrolyse weiterzuentwickeln. Im Zentrum der Forschung steht die Entwicklung einer völlig neuen Generation von Stacks und Zellen, die speziell für eine effiziente Massenproduktion optimiert sind.
Innerhalb des Projekts entwickeln die Partner Technologien, die es ermöglichen, die Zusammenstellung von Stacks vollständig zu automatisieren. Der Einsatz von Robotik soll dabei helfen, sowohl die Fertigungsprozesse als auch die bisher manuellen Montageabläufe zu verbessern.
Darüber hinaus arbeiten die Partner an der Optimierung der Lieferkette, um den Anforderungen einer industriellen Serienfertigung gerecht zu werden. Das Hauptziel von INSTALL AWE ist es, die Produktionskapazitäten der Elektrolyse erheblich zu steigern und gleichzeitig die Herstellungskosten zu reduzieren.
Langtitel: |
Industrialisierung der alkalischen Wasserelektrolyse |
Förderkennzeichen: |
03HY119A-D |
Gesamtfördersumme: |
ca. 19,9 Mio. Euro |
Partner: |
nucera AG, De Nora, Hoedtke GmbH, TU Braunschweig, BIAS, RWTH Aachen |
Projektlaufzeit: |
01.04.2021 – 31.12.2025 |
Kontakt in das Projekt: |
Peter Toros / Dr. Emile Ojong |
NCALab konzentriert sich auf kurzfristige Verbesserungen in der Produktion alkalischer Elektrolyseure durch punktuelle Automatisierungslösungen und Prozessoptimierungen.
Das Projekt NCALab konzentriert sich auf kurzfristig umsetzbare Verbesserungs-Maßnahmen. Innerhalb eines Zeitrahmens von zwei bis drei Jahren werden durch den gezielten Einsatz industrietauglicher Automatisierungslösungen Prozesse verbessert, von denen bereits laufende Elektrolyseprojekte profitieren können.
Selbst in Bereichen, in denen die Zellmontage derzeit noch vollständig manuell erfolgt, sollen durch punktuelle Verbesserungen und teilweise Automatisierung höhere Durchsatzraten, eine verbesserte Reproduzierbarkeit und geringere Kosten erreicht werden. Die Ergebnisse aus NCALab tragen dazu bei, die Pläne für die zukünftige Großserienmontage der AWE-Zellen zu verfeinern. Zudem liefern sie wichtige Erkenntnisse über den möglichen Automatisierungsgrad und die erzielbaren Produktionskennzahlen.
Langtitel: |
Nucera Assembly Lab |
Förderkennzeichen: |
03HY132 |
Gesamtfördersumme: |
ca. 1,3 Mio. Euro |
Partner: |
nucera AG |
Projektlaufzeit: |
01.03.2023 – 31.12.2025 |
Kontakt in das Projekt: |
Dr. Felix Gabriel |
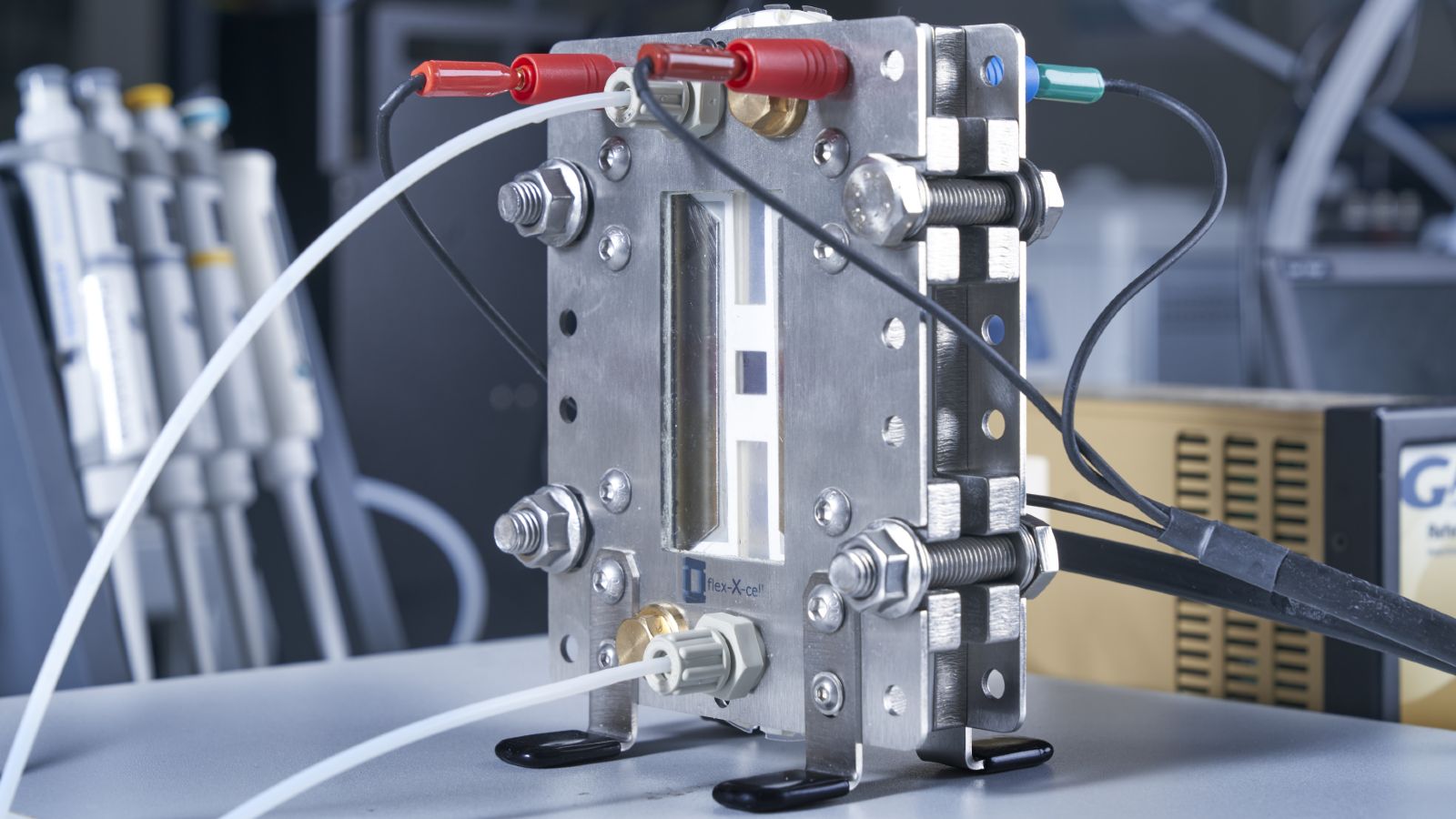
Next-Generation-Scale-up-Projekte: Neueste Verfahren werden hochskaliert
Einige Arten von Elektrolyseuren sind heute bereits so weit entwickelt, dass sie in Serienproduktion gehen könnten. Dabei gibt es weitere Elektrolyse-Verfahren, die ebenfalls vielversprechend sind. Manche kommen ganz ohne Edelmetalle aus, andere sind hoch effizient. Deswegen widmen sich drei H2Giga-Projekte im Next Generation Scale-up den Technologien von morgen und übermorgen. Ziel ist es, neue Verfahren weiterzuentwickeln und im größeren Maßstab zu testen. Zudem erarbeiten die Partner in diesem Bereich neue Designs verschiedener Elektrolyseur-Komponenten, um künftig Herstellungskosten zu reduzieren und die serielle Fertigung zu vereinfachen.
Das Projekt StaR adressiert Herausforderungen bei der kostengünstigen Herstellung von Elektrolyse-Stacks. Durch ein neues Stack-Design, das auf kostengünstigen Materialien und produktionsorientierten Fertigungsverfahren basiert, sollen Investitionskosten deutlich gesenkt werden, ohne die Leistung zu beeinträchtigen.
Die alkalische Wasserelektrolyse ist die älteste und eine der technisch ausgereiftesten Methoden zur Wasserstoffproduktion. Trotz ihrer langen Lebensdauer und hohen Zuverlässigkeit steht die Technologie vor Herausforderungen, insbesondere bei der serienmäßigen Produktion von Elektrolyse-Stacks. Als zentrale Komponenten sind die Stacks entscheidend für die Effizienz der Anlagen. Um den zukünftigen hohen Bedarf an wirtschaftlich erzeugtem Wasserstoff zu decken, müssen sie kostengünstig, aber dennoch hochpräzise gefertigt werden.
Das Projekt StaR nimmt sich dieser Herausforderung an, indem es ein neues Stack-Design entwickelt, das die Investitionskosten erheblich senkt. Durch den Einsatz von kostengünstigen Materialien und fortschrittlichen und zum Teil automatisierten Fertigungsverfahren wird eine drastische Reduktion der Herstellungskosten angestrebt, ohne dabei die Leistungsfähigkeit zu senken.
Um die Leistung und Zuverlässigkeit der neu entwickelten Stacks zu prüfen, wurde ein spezielles Testfeld an der TU Clausthal in Goslar eingerichtet. Hier können die Stacks unter realen Betriebsbedingungen getestet werden, indem sowohl die alltäglichen Belastungen als auch der dynamische Betrieb simuliert wird.
Die bisherigen Ergebnisse sind vielversprechend und zeigen, dass das innovative Stack-Design nicht nur die Herstellungskosten senkt, sondern auch wettbewerbsfähige Leistung bietet. Damit wird es zum Schlüssel für die zukünftige Skalierung und Kosteneffizienz von Wasserelektrolyseanlagen.
Langtitel: |
Stack Revolution: Reduktion der Kosten für alkalische Elektrolyseure auf einen Wert unter den Prognosen für 2030 |
Förderkennzeichen: |
03HY102A-E |
Gesamtfördersumme: |
ca. 22,6 Mio. Euro |
Partner: |
WEW GmbH, Technische Hochschule Clausthal, Hochschule Rhein-Waal, Ostbayerische Technische Hochschule Regensburg, Rheinisch-Westfälische Technische Hochschule Aachen |
Projektlaufzeit: |
01.04.2021 – 31.12.2025 |
Kontakt in das Projekt: |
Dr. Wiebke Lüke |
Das StacIE-Projekt konzentriert sich auf die Optimierung und den Scale-Up der Schlüsselkomponenten von Stacks für die PEMWE, um der Produktion von PEM-Elektrolyse-Stacks den Weg zu Gigawatt-Kapazitäten zu ebnen. Das Projekt verfolgt innovative Ansätze aus den Bereichen Simulation, Material- und Beschichtungsentwicklung, die bereits in kommerziell verfügbare Schaeffler-PEMWE-Stacks eingeflossen sind.
Ein PEM-Stack besteht aus mehreren übereinander gestapelten Elektrolysezellen, die das Kernelement dieser Technologie darstellen. Jede Zelle enthält unter anderem eine Membran mit Katalysatorbeschichtung, in und auf der die funktionellen elektrochemischen Reaktionen stattfinden.
Das Ziel von StacIE ist es, optimierte Kombinationen von Membranen, Katalysatorschichten, Bipolarplatten (BPP), porösen Transportschichten (PTL) und Dichtungen zu entwickeln. Diese Kombinationen sollen nicht nur kostengünstig und effizient, sondern auch für die industrielle Massenfertigung geeignet und im Einsatz robust sein. Durch die Erforschung und Entwicklung neuer Fertigungsmethoden und den Bau von Demonstratoren in einer Testumgebung treibt StacIE die Vorbereitungen für die Großserienproduktion voran.
Im Rahmen des seit drei Jahren laufenden Projekts StacIE wurden Validierungsmethoden erarbeitet, um Materialien und Materialzustände in elektrochemischer Umgebung zuverlässig beurteilen und vergleichen zu können. Ebenso wurden FEM- und CFD-Methoden erarbeitet und Simulationen zur Bewertung und Optimierung von Fertigung und Funktion umformtechnisch hergestellter Stack-Bauteile wie BPPs oder Rahmen mit unterschiedlichsten Umformelementen und Strömungsstrukturen durchgeführt.
Neue PTL-Systeme inklusive deren Beschichtung werden laufend variiert und validiert. Die gewonnenen Erkenntnisse fließen auch in die Optimierung der bereits kommerziell verfügbaren Schaeffler-Stacks ein. Zudem wurden angespritzte Dichtungen als Alternative zur Montage von O-Ringen zur Abdichtung gegen die bei der PEMWE eingesetzten Medien entwickelt.
Die gesammelten Erkenntnisse und eine optimale Verpaarung aller aktiven Komponenten eines PEM-Stacks tragen dazu bei, die Strömungsverluste zu reduzieren, die Effizienz der Stacks zu steigern und Robustheit und Dichtheit, und damit auch die Sicherheit, über die Lebensdauer zu erhöhen. Durch die Bemühungen um massentaugliche und standardisierte Stack-Technologien, verkürzte Entwicklungszeiten und beschleunigtes Scale-Up leistet das Projekt wesentliche Beiträge zur Industrialisierung der PEM-Wasser-Elektrolyse und bereitet die Lieferketten auf den erwarteten Bedarf in Großserien vor.
Langtitel: |
Stack Scale-up – Industrialisierung PEM Elektrolyse |
Förderkennzeichen: |
03HY103A-J |
Gesamtfördersumme: |
ca. 16,2 Mio. Euro |
Partner: |
Schaeffler Technologies AG & Co. KG, RWTH Aachen, Karlsruher Institut für Technologie, KCS Europe GmbH, TU Illmenau, Fraunhofer Gesellschaft, Forschungszentrum Jülich, Heraeus Precious Metals, Fumatech |
Projektlaufzeit: |
01.04.2021 – 31.12.2025 |
Kontakt in das Projekt: |
Sascha Rüth |
Das Projekt HY-Core zielt darauf ab, die AEM-Elektrolyse vom Labormaßstab auf den Megawatt-Maßstab zu skalieren, indem es hohe Betriebsfestigkeit und Resilienz gewährleistet. Das modulare System besteht aus mehreren zuschaltbaren Stacks, was Flexibilität und eine kosteneffiziente Produktion von Wasserstoff direkt aus erneuerbaren Energiequellen ermöglicht.
Die AEM-Elektrolyse stellt die neueste Entwicklung in der Reihe der Elektrolysetechnologien dar. Ihr Ziel ist es, die Stärken der PEM-Elektrolyse, einschließlich der Verwendung einer Polymermembran, mit den Vorzügen der alkalischen Elektrolyse, vor allem der Vermeidung teurer Edelmetalle als Katalysatoren, zu kombinieren.
HY-Core widmet sich der Aufgabe, die AEM-Technologie vom Labormaßstab auf den Megawatt-Maßstab zu übertragen. Das System wird speziell für hohe Betriebsfestigkeit und Resilienz optimiert, um eine robuste und zuverlässige Funktion unter verschiedenen Betriebsbedingungen sicherzustellen.
Ein besonderer Fokus liegt auf dem modularen Aufbau des Systems, das aus vielen kleinen, je nach Bedarf zuschaltbaren Stacks besteht. Diese Flexibilität ermöglicht es dem Megawatt-Elektrolyseur, sich effektiv an Schwankungen im Stromangebot und im Wasserstoffbedarf anzupassen. Dadurch wird eine großskalige, ressourcenschonende und kosteneffiziente Produktion von Wasserstoff direkt an der Quelle erneuerbarer Energie möglich.
Langtitel: |
Entwicklung des ersten AEM-Elektrolyseurs der Megawattklasse |
Förderkennzeichen: |
03HY104A-B |
Gesamtfördersumme: |
ca. 13,3 Mio. Euro |
Partner: |
Enapter GmbH, FH Münster |
Projektlaufzeit: |
01.05.2021 – 30.09.2025 |
Kontakt in das Projekt: |
Florian Vogt |
Das Projekt IRIDIOS strebt für die PEM-Elektrolyse eine signifikante Reduzierung des Iridium-Gehalts an – und das nach wie vor bei einem hocheffizienten und langlebigen Betrieb. Hierfür erforscht das Projekt weitere Verbesserungen und Skalierungen von Iridium-armen Membran-Elektroden-Einheiten.
Iridium, ein kritischer Bestandteil der Katalysatorschicht der Anode in PEM-Elektrolyseuren, ist ein seltenes und kostbares Metall. Angesichts der wachsenden Nachfrage nach Grünem Wasserstoff und dem damit verbundenen Hochlauf der PEM-Elektrolyse auf Gigawatt-Kapazitäten, wird es immer wichtiger, Iridium effizient und sparsam zu verwenden.
Die Forscherinnen und Forscher von IRIDIOS konnten im Kopernikus-Projekts P2X erfolgreich eine Membran-Elektroden-Einheit entwickeln, die trotz eines signifikant verringerten Gehalts an Iridium eine gleichbleibende sehr gute Effizienz in der Elektrolyse zeigte. Innerhalb des größeren Forschungskontextes H2Giga werden diese Iridium-armen Membran-Elektroden-Einheiten nun unter praxisnahen Bedingungen und in drei unterschiedlichen Skalen hinsichtlich ihrer Effizienz und Stabilität verbessert und untersucht.
IRIDIOS gliedert sich in drei Hauptbereiche: die Skalierung der Komponenten, die Testung von Stacks und die Identifizierung von Betriebseffekten. Ziel ist es, in allen drei Bereichen den Übergang vom Labor- in den Pilotmaßstab zu demonstrieren. Somit strebt das Projekt an, die Voraussetzungen für den Gigawatt-Ausbau der PEM-Elektrolyse bis 2030 zu schaffen. Dabei wird besonderes Augenmerk auf die ökologischen und ökonomischen Auswirkungen der gesamten Prozesskette gelegt, um eine nachhaltige und wirtschaftlich tragfähige Produktion zu gewährleisten.
Langtitel: |
Ir-arme hocheffiziente MEA für PEM-Elektrolysestack im MW-Bereich |
Förderkennzeichen: |
03HY129A-F |
Gesamtfördersumme: |
ca. 5,3 Mio. Euro |
Partner: |
Heraeus Precious Metals GmbH & Co. KG, Technische Universität München, Ludwig-Maximilians-Universität München, Bayerisches Zentrum für Angewandte Energieforschung e. V., Greenerity GmbH, Quest One GmbH |
Projektlaufzeit: |
01.03.2023 – 31.12.2025 |
Kontakt in das Projekt: |
Dr. Christian Gebauer |
Das Projekt AEM-Direkt entwickelt fortschrittliche Beschichtungstechniken für AEM-Elektrolyseure zur effizienten iridiumfreien Wasserstoffproduktion. Es erforscht kostengünstige Methoden, um Katalysatoren direkt auf Membranen oder die porösen Transportschichten aufzutragen. Das Ziel ist es, diese Technologien grundlegend für die großflächige Anwendung zu untersuchen und in Richtung der elektrochemischen Leistungsfähigkeit zu optimieren.
Das Projekt AEM-Direkt konzentriert sich auf die Entwicklung fortschrittlicher Beschichtungstechniken für AEM-Elektrolyseure, die eine spezielle Art von Technologie zur Wasserstoffproduktion darstellen. Diese Elektrolyseure nutzen Membranen, die Hydroxid-Ionen leiten können, um effizient Wasserstoff zu erzeugen. Ein zentraler Aspekt des Projekts ist die Erforschung und Entwicklung von kostengünstigen Methoden, um Katalysatoren direkt auf diese Membranen oder die porösen Transportschichten aufzutragen. Das Elektrolyseurdesign wird an die jeweiligen Anforderungen in Bezug auf die Verortung des Katalysators angepasst.
Im Rahmen des Projekts werden verschiedene Techniken verglichen: Einige setzen auf Prozesse, bei denen die Katalysatoren aus der Gasphase aufgetragen werden – wie beim Aufdampfen oder thermischen Sprühen. Andere Methoden arbeiten mit Flüssigkeiten, bei denen die Pasten der Katalysatoren auf die Membran gestrichen oder gedruckt werden.
Das Ziel ist es, herauszufinden, welche dieser Techniken am besten für die großflächige Anwendung bei entsprechender Leitungsfähigkeit geeignet sind. Die ersten Experimente finden im kleinen Rahmen statt, aber das Ziel ist es, diese Technologien so weiterzuentwickeln, dass sie auf industrieller Ebene mit großen aktiven Flächen von bis zu 5000 cm² umgesetzt werden können. Dadurch soll die AEM-Technologie helfen, die Vorteile bisheriger Elektrolysemethoden (Polymer-Membran-Elektrolyse, iridiumfreie alkalische Elektrolyse) zu kombinieren und die Wasserstoffproduktion effizienter und kostengünstiger zu machen.
Langtitel: |
Direktbeschichtung von anionenleitenden Membranen für großskalige Wasserelektrolyseure |
Förderkennzeichen: |
03HY130A-I |
Gesamtfördersumme: |
ca. 14,3 Mio. Euro |
Partner: |
Siemens Energy Global GmbH & Co. KG, TU Berlin, Aalberts Surface Technologies GmbH, Deutsches Zentrum für Luft- und Raumfahrt e. V., Evonik Operations, Forschungszentrum Jülich GmbH, Schlötter GmbH, Fritz-Haber-Institut |
Projektlaufzeit: |
01.04.2023 – 28.02.2026 |
Kontakt in das Projekt: |
Dr. Günter Schmid |
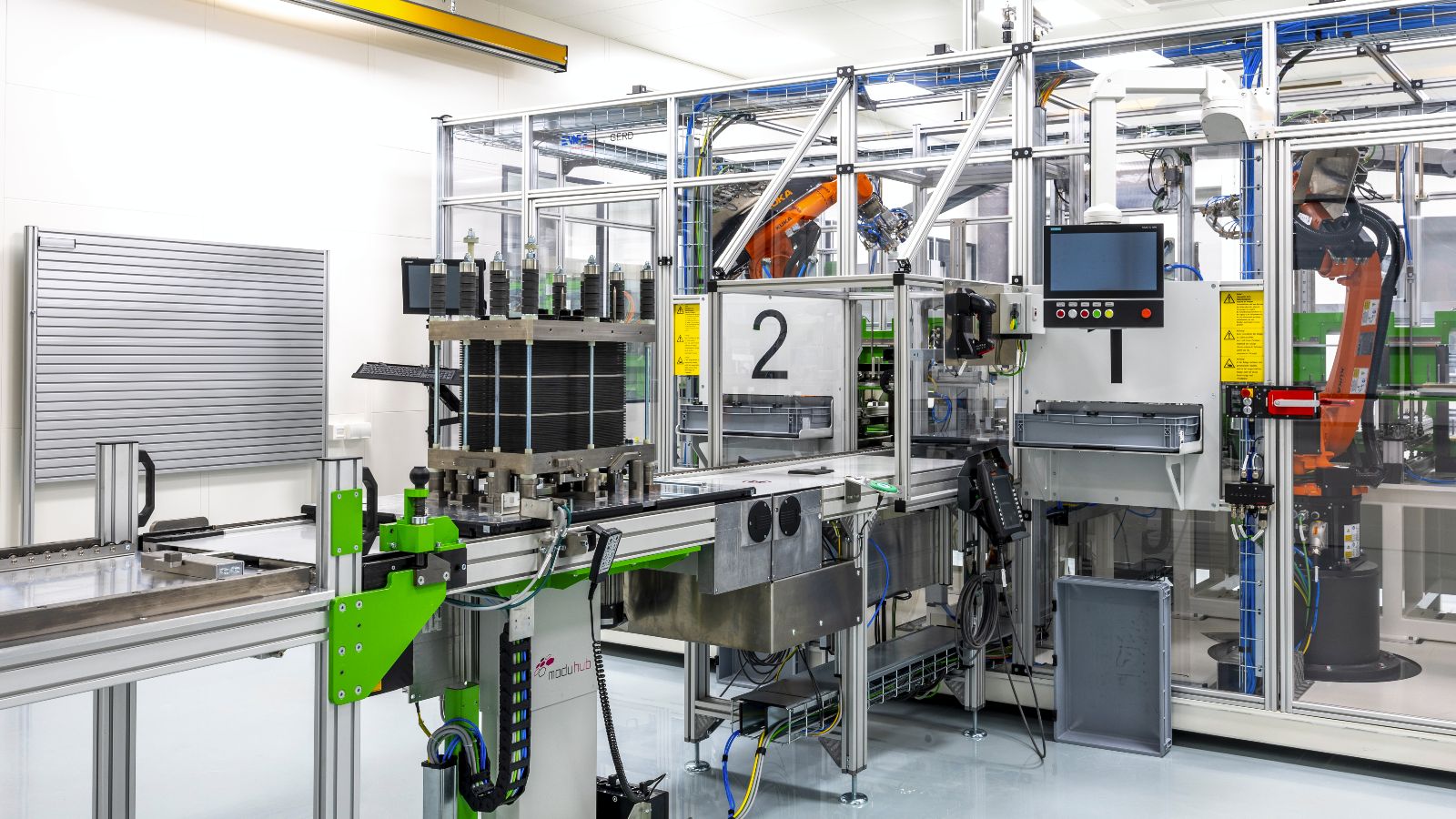
Innovationspool-Projekte: Wissenslücken schließen
Der wissenschaftsnahe Innovationspool untersucht und entwickelt übergreifende Verfahren, Technologien und Komponenten rund um die Elektrolyse. Insbesondere die Prüfung von neuen Materialien und Fertigungstechnologien steht im Fokus. Ebenso Fragen zu Lebensdauer, Recyclingfähigkeit und Automatisierungsmöglichkeiten. Zudem kann die Wirtschaft über den Innovationspool Forschungsbedarfe und Wissenslücken an die Wissenschaft kommunizieren. So wird gewährleistet, dass das Leitprojekt seine Innovationsfähigkeit behält.
Die Sauerstoffbildung an der Anode einer Elektrolysezelle hat einen wesentlichen Einfluss auf die Leistung der alkalischen Wasserelektrolyse und steht daher im Mittelpunkt der Forschung von PrometH2eus. Ziel ist es, Wege aufzuzeigen, wie die Entwicklung neuer Anodenmaterialien von Beginn an praxisorientiert gestaltet werden kann, um eine spätere effiziente und langzeitstabile industrielle Anwendung zu gewährleisten.
Die Materialsynthese wird dabei von modernsten Analytik- und Simulationsmethoden begleitet, welche permanent hinsichtlich ihres Einsatzes unter technisch-relevanten Bedingungen optimiert werden. Für aussichtsreiche Materialien werden dann Hochskalierungsverfahren weiterentwickelt. Deren Testung erfolgt zunächst im Labormaßstab mit Elektrodengrößen von 100 cm2 mit besonderem Fokus auf technisch-relevante Messbedingungen. Anschließend werden aus den vielversprechendsten Kandidaten Prototyp-Elektroden gefertigt und in industriellen Testständen validiert.
Insgesamt 26 Partner aus Industrie und Wissenschaft vereinen in diesem Projekt ihre Expertise in Syntheseverfahren und Analytikmethoden. Das im Projekt gewonnene Wissen wird zudem in einem Leitfaden für anwendungsorientierte Elektrodenentwicklung der wissenschaftlichen Gemeinschaft für zukünftige Forschung zur Verfügung gestellt.
Langtitel: |
Projektverbund zur optimierten Materialentwicklung für die technische H2-Erzeugung durch verbesserte Sauerstoffelektroden |
Förderkennzeichen: |
03HY105A-N |
Gesamtfördersumme: |
ca. 5,4 Mio. Euro |
Partner: |
RWTH Aachen University, Christian-Albrechts-Universität zu Kiel, Technische Universität Berlin, Max-Planck-Institut für Chemische Physik fester Stoffe, Max-Planck-Institut für Chemische Energiekonversion, Max-Planck-Institut für Kohlenforschung, Universität Duisburg-Essen, Technische Universität Darmstadt, Friedrich-Alexander-Universität Erlangen-Nürnberg, Max-Planck-Institut für Eisenforschung, ThyssenKrupp, Uhde Chlorine Engineers GmbH, De Nora Deutschland GmbH, Umicore AG & Co. KG, |
Projektlaufzeit: |
01.04.2021 – 30.09.2025 |
Kontakt in das Projekt: |
Anna Mechler und Vera Seidl |
Das Projekt Fluorfreie MEA widmet sich der Erforschung umweltfreundlicher Membranen für PEM-Elektrolyseure, die ohne Fluor auskommen. Diese neuen Membranen bieten eine kostengünstige und nachhaltige Alternative zu den üblicherweise verwendeten Membranen aus per- oder polyfluorierten Alkylpolymeren (PFAS). Mit dieser Innovation trägt das Projekt maßgeblich zur Weiterentwicklung der nächsten Generation von PEM-Wasserelektrolyseuren bei.
Die Membran-Elektroden-Einheit, kurz MEA, ist das Herz der Elektrolysezelle. Bei der PEM-Elektrolyse werden als Membran üblicherweise Polymere auf Basis von Perfluorsulfonsäuren (PFSA) verwendet. Man kann sich dieses Material als PTFE (Polytetrafluorethylen, Handelsname z. B. Teflon®) mit angehängten Säuregruppen vorstellen. Letztere sorgen für die protonische Leitfähigkeit, während das PTFE-Rückgrat mechanische Stabilität und Integrität gewährleistet. Diese Materialien sind – typisch für perflourierte Stoffe – chemisch außerordentlich stabil und halten den aggressiven Bedingungen in der Elektrolysezelle stand. Sie haben aber auch Nachteile: die aufwändige Fluorchemie macht ihre Herstellung teuer. Auch Entsorgung oder Recycling der Membran selbst bzw. der angrenzenden Katalysatorschichten wird durch die Gegenwart fluorierter Materialien schwieriger. Zudem werden derzeit Restriktionen von PFAS in der EU geprüft.
Wünschenswert wäre daher ein protonenleitendes Membranmaterial, das nicht fluoriert ist, aber dennoch hohe Leistung und Langzeitstabilität bietet. Das Projekt Fluorfreie-MEA erforscht und entwickelt solche Membranmaterialien. Neueste Membranen, die auf fluorfreien Polymeren basieren, haben bereits vielversprechende Ergebnisse gezeigt. Sie bieten eine wesentlich bessere Barriere gegen unerwünschten Gasübertritt als PFSA-Membranen und gewährleisten eine sehr hohe Spannungseffizienz. Im Rahmen dieses Projekts arbeiten Industrie- und Wissenschaftspartner gemeinsam daran, leistungsfähige fluorfreie MEAs mit skalierbaren Technologien zu entwickelt, um die nächste Generation von effizienten und kostengünstigen Wasserelektrolyseuren zu ermöglichen.
Langtitel: |
Fluorfreie Membran-Elektroden-Einheiten mit hoher Effizienz, geringerem Gasübertritt und langer Lebensdauer zur nachhaltigen Erzeugung von Wasserstoff |
Förderkennzeichen: |
03HY106A-C |
Gesamtfördersumme: |
ca. 6,3 Mio. Euro |
Partner: |
Hahn-Schickard-Gesellschaft für angewandte Forschung e. V., FUMATECH BWT GmbH, Albert-Ludwigs-Universität Freiburg |
Projektlaufzeit: |
01.04.2021 – 31.12.2025 |
Kontakt in das Projekt: |
Dr. Carolin Klose |
IREKA zielt darauf ab, den Iridiumanteil in PEM-Elektrolyseuren zu reduzieren, ohne die Leistung und Stabilität zu beeinträchtigen. Neue Katalysatormaterialien und Herstellungsverfahren werden entwickelt, um mit weniger Iridium eine große katalytische Aktivität zu erreichen.
PEM-Elektrolyseure, die zur Wasserstoffherstellung eingesetzt werden, nutzen üblicherweise das seltene und teure Edelmetall Iridium als Katalysator. Angesichts des wachsenden Bedarfs an Wasserstoff und der begrenzten Verfügbarkeit von Iridium, steht die Industrie vor der Herausforderung, effiziente Alternativen zu entwickeln, um die Abhängigkeit von diesem Material zu verringern.
Das Projekt IREKA widmet sich der Entwicklung neuer Katalysatormaterialien, die den Iridiumgehalt in den Anoden von PEM-Elektrolyseuren reduzieren, ohne die Leistung und Stabilität zu beeinträchtigen. IREKA nutzt innovative Methoden um das Iridium besser zu verteilen und damit zugänglicher für die Wasserspaltung zu machen. Die Methoden zielen auch auf die Entwicklung von Metallmischungen und verbesserten Materialformen ab, um die Effizienz der Katalyse zu steigern und den Einsatz von teurem Iridium zu reduzieren. Zusätzlich werden neue Herstellverfahren für katalytisch aktive Beschichtungen entwickelt, die zur Kostensenkung und Nachhaltigkeit der PEM-Elektrolyse beitragen sollen.
Langtitel: |
Iridium-reduzierte Anodenkatalysatoren für die PEM-Wasserelektrolyse |
Förderkennzeichen: |
03HY107A-B |
Gesamtfördersumme: |
ca. 1,07 Mio. Euro |
Partner: |
Leibniz-Institut für Katalyse e. V., Fraunhofer IPA |
Projektlaufzeit: |
01.04.2021 – 30.09.2024 |
Kontakt in das Projekt: |
Dr. Annette-Enrica Surkus |
Das Projekt HyThroughGen verwendet Hochdurchsatzverfahren, um die Entwicklung neuer Materialien und wichtiger Zellkomponenten für die PEM-Elektrolyse zu beschleunigen. Ziel ist es, Entwicklungszyklen von bis zu zehn Jahren auf zwei bis drei Jahre zu verkürzen, indem vielversprechende Materialkombinationen schnell identifiziert und validiert werden.
HyThroughGen zielt darauf ab, die Entwicklungszeiten für neue Materialien in der PEM-Elektrolyse drastisch zu verkürzen. Während die Entwicklung neuer Materialien für die Elektrolyse normalerweise bis zu zehn Jahre dauert, strebt HyThroughGen an, diesen Prozess auf nur zwei bis drei Jahre zu reduzieren.
Im Mittelpunkt stehen dabei Hochdurchsatzverfahren, mit denen schnell große Mengen an Membran- und Elektrodenmaterialien getestet werden können. Diese sind zentrale Bestandteile der Membran-Elektroden-Einheit, dem Herzstück jeder Elektrolysezelle. Durch die Erstellung von Material- und Komponentenbibliotheken und die anschließende Charakterisierung dieser Materialien hinsichtlich Leistung und Langzeitstabilität können vielversprechende Kandidaten schnell identifiziert und validiert werden.
Durch die Kombination von Experimenten, Auswertungen und Simulationen beschleunigt HyThroughGen den Innovationsprozess, um schnellere Fortschritte bei der Entwicklung effizienterer und haltbarerer Materialien für die Wasserelektrolyse zu ermöglichen.
Langtitel: |
Beschleunigung der Entwicklungszyklen für die Wasserelektrolyse mit saurer Festelektrolytmembran durch Hochdurchsatzverfahren |
Förderkennzeichen: |
03HY108A-D |
Gesamtfördersumme: |
ca. 12,27 Mio. Euro |
Partner: |
Forschungszentrum Jülich GmbH, Fraunhofer ISE, Leibniz Universität Hannover, Technische Universität Berlin |
Projektlaufzeit: |
01.05.2021 – 31.03.2025 bzw. |
Kontakt in das Projekt: |
Prof. Dr. Simon Thiele und Dr. Dominik Dworschak |
AlFaKat fokussiert sich auf die Entwicklung elektrochemischer Katalysatoren für die AEM-Elektrolyse. Kern der Forschung ist die PVD-Pulverbeschichtung zur Herstellung von Core-Shell-Katalysatoren. Diese Technologie soll die kostengünstige und großtechnische Produktion von Katalysatoren für die AEM-Elektrolyse ermöglichen.
In diesem Projekt liegt der Fokus auf der Weiterentwicklung von elektrochemischen Katalysatoren, die speziell für die AEM-Elektrolyse verwendet werden. Ein zentraler Aspekt des Projekts ist die Erforschung und Optimierung von Herstellungsverfahren, um eine großskalige und kontinuierliche Produktion dieser Katalysatoren zu ermöglichen.
Als Schlüsseltechnologie wird dabei die PVD-Pulverbeschichtung (Physical Vapour Deposition) eingesetzt. Dieses Verfahren ermöglicht die Herstellung von sogenannten Core-Shell-Katalysatoren, bei denen eine aktive Katalysatorschicht auf ein Trägersubstrat aufgebracht wird. Diese Katalysatoren werden anschließend für die Herstellung der Membran-Elektroden-Einheiten verwendet. Diese Einheiten werden unter Bedingungen getestet, die echten Anwendungen nahekommen.
Durch die Verwendung von skalierbarer PVD-Technologie und kostengünstigen, unedlen Übergangsmetallen als aktive Komponenten zielt das Projekt darauf ab, eine effiziente und wirtschaftlich attraktive Produktion von Katalysatoren für AEM-Elektrolyseure zu realisieren.
Langtitel: |
Neuartige Katalysatoren für AEM-WE Membran-Elektroden-Einheiten |
Förderkennzeichen: |
03HY109A-C |
Gesamtfördersumme: |
ca. 2,11 Mio. Euro |
Partner: |
Zentrum für Brennstoffzellen-Technik GmbH, RWTH Aachen, KCS Europe GmbH |
Projektlaufzeit: |
01.04.2021 – 31.12.2025 |
Kontakt in das Projekt: |
Dr. Moritz Pilaski |
Degrad-El3 untersucht Degradationsmechanismen und erstellt Lebensdauervorhersagen für verschiedene Elektrolysetechnologien. Durch beschleunigte Alterungstests und den Einsatz von KI-Technologien sollen Materialien schneller entwickelt und ihre Langzeitstabilität besser eingeschätzt werden.
Elektrolysezellen sind entscheidend für die effiziente Produktion von Wasserstoff, doch sie müssen auch über Jahre hinweg zuverlässig funktionieren. Das Projekt Degrad-El3 fokussiert sich darauf, die Lebensdauer von Materialien für Elektrolysezellen schneller und effizienter zu bewerten, ohne sie jahrelang unter realen Bedingungen testen zu müssen.
Im Projekt werden für die PEM-Elektrolyse, die alkalische Elektrolyse und die Hochtemperaturelektrolyse systematische Untersuchungen durchgeführt. Dabei werden Materialien und Komponenten in Einzelzellen oder Short-Stacks unter extremen Bedingungen getestet, um Degradationsprozesse zu beschleunigen und besser verstehen zu können. Die Ergebnisse dieser Tests werden durch detaillierte Analysen ergänzt, die Aufschluss über die verschiedenen Degradationsmechanismen geben.
Zur Unterstützung der Forschungsarbeit setzt das Projekt auf fortschrittliche Technologien wie künstliche neuronale Netze, Quantencomputing und hybride Machine-Learning-Methoden. Das Ziel von Degrad-El3 ist es, die Langzeitstabilität der untersuchten Materialien vorherzusagen und so die Entwicklungszeiten für neue, langlebige Elektrolysematerialien deutlich zu verkürzen.
Langtitel: |
Identifizierung von Degradations-Mechanismen bei PEMEL-, AEL- und HTEL-Elektrolyseuren |
Förderkennzeichen: |
03HY110A-E |
Gesamtfördersumme: |
ca. 7,8 Mio. Euro |
Partner: |
Dechema-Forschungsinstitut, Deutsches Zentrum für Luft- und Raumfahrt e. V., Europäisches Institut für Energieforschung EifER, Fraunhofer-Institut für Produktionstechnik und Automatisierung (IPA), Zentrum für BrennstoffzellenTechnik GmbH |
Projektlaufzeit: |
01.04.2021 – 31.12.2025 |
Kontakt in das Projekt: |
Dr. Jean-Francois Drillet |
ReNaRe entwickelt Technologien für das Recycling von PEM- und Hochtemperatur-Elektrolyseuren. Das Projekt zielt darauf ab, spezifische Prozessschema zu erstellen, die zukünftig Recycling im technischen Maßstab ermöglichen und flexibel auf technologische Entwicklungen reagieren können.
Das Projekt ReNaRe widmet sich der wichtigen Aufgabe, nachhaltige Recyclingmethoden für Elektrolyseure zu entwickeln. Ziel ist es, am Ende der Nutzungsdauer von PEM- und Hochtemperatur-Elektrolyseuren die wertvollen Materialien und kritischen Rohstoffe zurückzugewinnen und der Wiederverwertung zuzuführen.
Im Projekt arbeiten Forschung und Industrie eng zusammen, um Technologien zu entwickeln, die es ermöglichen, die Stacks dieser Elektrolyseure zu demontieren und die verschiedenen Materialien effizient zu trennen. Dabei kommen innovative Ansätze aus den Bereichen der Funktionsmaterialien, automatisierte Demontage, mechanisches und sensorgestütztes Recycling sowie Metallurgie zum Einsatz.
ReNaRe strebt danach, für jede der untersuchten Elektrolysetechnologien ein Recyclingverfahren zu entwickeln, das prinzipiell in einem technischen Maßstab umsetzbar ist und gleichzeitig flexibel genug, um auf die zukünftigen dynamischen technologischen Entwicklungen reagieren zu können. Zusätzlich werden in Lebenszyklusanalysen und technoökonomische Studien die Recyclingansätze hinsichtlich Nachhaltigkeit und Kosteneffizienz quantitativ bewertet, um ganzheitliche wirtschaftliche Aussagen über den Kreislauf der wertvollen und kritischen Ressourcen zu erarbeiten.
Langtitel: |
Recycling – Nachhaltige Ressourcennutzung |
Förderkennzeichen: |
03HY111A-E, G-J und L |
Gesamtfördersumme: |
ca. 8,6 Mio. Euro |
Partner: |
Technische Universität Bergakademie Freiberg, Karlsruher Institut für Technologie, Fraunhofer IPA, Helmholtz-Zentrum Dresden-Rossendorf e. V., RWTH Aachen, Heraeus Precious Metals GmbH & Co. KG, Öko-Institut. Institut für angewandte Ökologie e. V., DECHEMA e. V., Forschungszentrum Jülich GmbH, Technische Universität München |
Projektlaufzeit: |
01.04.2021 – 30.09.2025 |
Kontakt in das Projekt: |
Prof. Dr.-Ing. Urs Alexander Peuker |
FRHY konzipiert Lösungen für die großserientaugliche Fertigung von PEM-Elektrolyseuren. Das Projekt umfasst die Entwicklung eines Referenzstacks sowie neuer Produktions- und Prüfmodule bzw. deren digitale Abbilder, um Fertigungsqualität, Skalierbarkeit und Kosten zu optimieren.
Das Projekt FRHY entwickelt innovative Lösungen für die Massenproduktion von PEM-Elektrolyseuren. Ziel ist es, neue Produktions- und Prüfmodule zu entwickeln und deren digitale Abbilder in einer zentralen virtuellen Architektur zu integrieren. Dieser Ansatz schafft einen Technologiebaukasten, der es ermöglicht, verschiedene Fertigungsverfahren hinsichtlich ihrer Qualität, Skalierbarkeit und Kosten direkt zu vergleichen.
Mit diesem modularen System können Produktvarianten effizient zusammengestellt und bewertet werden, was eine umfassende Analyse der gesamten Wertschöpfungskette ermöglicht. So können Strategien zur Parallelisierung, Automatisierung und Optimierung der Fertigungstiefe entwickelt werden. Dies bietet eine solide Entscheidungsgrundlage für Investitionen und die Bewertung des Return on Investment in Abhängigkeit von der geplanten Produktionsmenge.
Darüber hinaus entwickelt das Projekt neue Zelldesigns, die auf industrielle Massenfertigung ausgelegt sind. Deren Kernkomponenten werden mit fortschrittlichen kontinuierlichen Fertigungsmethoden hergestellt. So konnten die Projektbeteiligten den FRHY-Referenzstack bereits aufgebauen. Dieser zeigt die Wirksamkeit von konsequentem Design for Manufacturing and Assembly und dient als Basis für den gezielten Wissens- und Technologietransfer.
Das Projekt trägt wesentlich dazu bei, die Produktion von Elektrolysekomponenten kosteneffizient, durchgängig und skalierbar zu machen, was die technischen und wirtschaftlichen Eigenschaften der Produkte erheblich verbessert.
Langtitel: |
ReferenzFabrik für hochratenfähige Elektrolyseur-Produktion |
Förderkennzeichen: |
03HY112A-E |
Gesamtfördersumme: |
ca. 26,5 Mio. Euro |
Partner: |
Fraunhofer-Institut für Werkzeugmaschinen und Umformtechnik (IWU), Fraunhofer-Institut für Produktionstechnologie (IPT), Fraunhofer-Institut für Produktionstechnik und Automatisierung (IPA), Fraunhofer-Institut für Elektronische Nanosysteme (ENAS), Fraunhofer-Institut für Windenergiesysteme (IWES) |
Projektlaufzeit: |
01.04.2021 – 31.12.2025 (Teilprojekte enden früher) |
Kontakt in das Projekt: |
Dr. Ulrike Beyer |
FertiRob entwickelt Technologien für die (teil-)automatisierte Serienfertigung von Elektrolyseuren. Das Projekt umfasst die Erstellung digitaler Zwillinge für Produkte und Anlagen, um die Qualitätssicherung zu unterstützen und Produktionsprozesse zu optimieren.
Das Projekt FertiRob zielt darauf ab, Technologien für die Serienfertigung von Elektrolyseuren zu entwickeln, die einen automatisierten Zusammenbau der Produktionskomponenten ermöglichen. Dabei konzentriert sich das Projekt nicht nur auf die physischen Aspekte wie den Aufbau verschiedener Demonstrationsanlagen für Teilprozesse, sondern auch auf die digitalen Komponenten der Produktionsstätte.
Durch einen modulbasierten Ansatz wird die Planung der Produktionsanlagen mit einem Konfigurator erleichtert. Zudem werden sowohl ein digitaler Produkt- als auch ein Anlagenzwilling erstellt, die während des Betriebs mit echten Daten aktualisiert werden können. Diese digitalen Zwillinge tragen zur Qualitätssicherung und Nachverfolgung bei und ermöglichen es, Ergebnisse schnell und materialsparend zu erzielen.
Bevor der physische Aufbau beginnt, ermöglicht FertiRob das virtuelle Testen der gesamten Anlagenarchitektur, was eine kostensparende und effiziente Vorgehensweise darstellt. Die durch FertiRob entwickelten Technologien sollen die Automatisierung in der Produktion fördern und damit die Herstellungsmengen wichtiger Komponenten erhöhen.
Langtitel: |
Fertigung und Robotik |
Förderkennzeichen: |
03HY113A-P |
Gesamtfördersumme: |
ca. 19 Mio. Euro |
Partner: |
Ruhr-Universität Bochum, RIF Institut für Forschung und Transfer e. V., Karlsruher Institut für Technologie, J. Schmalz GmbH, EKS InTec GmbH, ABB AG, FFT Produktionssysteme GmbH & Co. KG, AUTOMATION W + R GmbH, Boll Automation GmbH, Autoproc GmbH & Co. KG, ISRA VISION AG, ESSERT GmbH, inpro Innovationsgesellschaft für fortgeschrittene Produktionssysteme in der Fahrzeugindustrie mbH, let’s dev GmbH & Co. KG, IBG Automation GmbH, Robert Bosch GmbH |
Projektlaufzeit: |
01.04.2021 – 31.03.2025 (teilweise bis 30.09.2025) |
Kontakt in das Projekt: |
Prof. Dr.-Ing. Bernd Kuhlenkötter |
HyPLANT100 fokussiert sich auf die Optimierung und Automatisierung beim Aufbau großer Elektrolyseanlagen. Es erforscht den Einsatz von Robotik und digitaler Unterstützung in der Montage, um die Produktionsprozesse effizienter und flexibler zu gestalten.
Das Projekt HyPLANT100 konzentriert sich auf die Forschung und Entwicklung optimierter sowie automatisierter Verfahren zur Errichtung großer Elektrolyseanlagen. Innerhalb des H2Giga-Leitprojekts bildet HyPLANT100 die Brücke zwischen der Herstellung kleinster Baueinheiten der Elektrolyseure und der Installation großskaliger Gesamtsysteme am Einsatzort.
Im Projekt werden Elektrolyse-Grundeinheiten in einer teilautomatisierten Produktion zu modularen Baugruppen, den sogenannten Skids, zusammengebaut. Dabei wird besonders darauf geachtet, wo Robotik und Mensch-Maschine-Kollaboration effizient eingesetzt werden können. Ein weiteres Kernziel ist die Digitalisierung und intelligente Unterstützung der Montageprozesse, von der Vormontage bis hin zur Endinstallation im Feld, unterstützt durch fortschrittliche Sensorik und mobile Robotik.
Diese Skids werden anschließend vor Ort zu einem vollständigen System kombiniert, wobei die Systemkonfiguration modular gestaltet wird, um flexibel auf die Anforderungen des jeweiligen Standorts reagieren zu können. Ein besonderer Fokus liegt dabei auf einer platzsparenden Bauweise, um die Flächenversiegelung so gering wie möglich zu halten.
Zusätzlich umfasst HyPLANT100 bereichsübergreifende Themen wie Standardisierung und Qualifizierung. Hier werden Standards für Komponenten und Prozesse entwickelt, um Kosten zu senken und Offenheit gegenüber verschiedenen Herstellern und Technologien zu gewährleisten. Im Bereich der Qualifizierung werden Schulungsinhalte erarbeitet, die Fachkräfte gezielt auf die spezifischen Anforderungen der Wasserstoffindustrie vorbereiten sollen.
Langtitel: |
Entwicklung optimierter und automatisierter Abläufe und Standards für den Aufbau großskaliger Wasserelektrolyseure |
Förderkennzeichen: |
03HY114A-G und I |
Gesamtfördersumme: |
ca. 6,6 Mio. Euro |
Partner: |
Entwicklungsagentur Region Heide AöR, Ruhr-Universität Bochum, Technische Universität Hamburg, IBG Technology Hansestadt Lübeck GmbH, Fest GmbH, H2 Core Systems GmbH, Advanced Training Technologies GmbH, HYPION GmbH |
Projektlaufzeit: |
01.04.2021 – 31.12.2025 |
Kontakt in das Projekt: |
Martin Eckhard |
SYSTOGEN100 entwickelt eine Softwareplattform zur Steuerung von großskaligen Elektrolyseuren und anderen Energiesystemkomponenten. Ziel ist die Optimierung des Betriebs und der Auslegung unter Berücksichtigung wechselnder Energieverfügbarkeit und Nachfrage.
Das Projekt SYSTOGEN100 adressiert eine zentrale Herausforderung der zukünftigen Energieversorgung: Die effiziente Integration und Steuerung von Elektrolyseuren in das Energiesystem, um die schwankende Einspeisung aus erneuerbaren Energiequellen optimal zu nutzen. Ziel ist es, eine Softwareplattform zu entwickeln, die großskalige Elektrolyseanlagen und andere Komponenten des Energiesystems steuert, um einen möglichst ökonomischen und effizienten Betrieb sicherzustellen.
Die Plattform berücksichtigt dabei nicht nur aktuelle Wetterdaten und Strompreise, sondern auch Verbrauchsdaten und Prognosen zu Lasten und Einspeisungen, um die Elektrolyseanlagen stets optimal zu betreiben. Zusätzlich zu dieser innovativen Steuerungstechnologie entwickelt SYSTOGEN100 ein Kapitalmarkttool zur dynamischen Risikomodellierung. Dieses Tool unterstützt Investitionsentscheidungen, indem es Transparenz schafft und Investoren hilft, die Risiken und Chancen in der Wasserstoffwirtschaft besser zu bewerten.
Darüber hinaus werden im Rahmen von SYSTOGEN100 Handlungsempfehlungen im rechtlichen Bereich erarbeitet, um sicherzustellen, dass die technisch und wirtschaftlich optimierten Systemlösungen auch rechtlich umsetzbar sind. Damit leistet das Projekt einen wichtigen Beitrag zur Gestaltung eines nachhaltigen und effizienten Energiesystems der Zukunft.
Langtitel: |
Vollständige Orchestrierung der Systemkomponenten für eine effiziente grüne Wasserstoff-Infrastruktur |
Förderkennzeichen: |
03HY115A-C und E-F |
Gesamtfördersumme: |
ca. 3,8 Mio. Euro |
Partner: |
Entwicklungsagentur Region Heide AöR, Fichtner IT Consulting GmbH, Tachycon GmbH, Deutsches Zentrum für Luft- und Raumfahrt e. V., Fachhochschule Westküste - Hochschule für Wirtschaft und Technik |
Projektlaufzeit: |
01.04.2021 – 31.12.2025 |
Kontakt in das Projekt: |
Martin Eckhard |
eModule erforscht modulare und skalierbare Betriebskonzepte für Elektrolyseure. Es fokussiert auf die Automatisierung und die Optimierung der Effizienz von Elektrolyseanlagen mittels Agentensystemen und digitalen Zwillingen.
Das Projekt eModule widmet sich der Entwicklung von fortschrittlichen Betriebskonzepten für Elektrolyseanlagen, die in direkter Nähe zu den Verbrauchern dezentral und flexibel Wasserstoff produzieren. Ziel ist es, die Anlagen so zu gestalten, dass sie dynamisch auf zeitliche und örtliche Anforderungen reagieren können.
Im Zentrum des Projekts stehen die Automatisierung und die Skalierbarkeit der Elektrolyseure. Es werden neue Steuerungskonzepte entwickelt, um die Effizienz und Integration der Anlagen in bestehende Infrastrukturen zu optimieren. Durch den Einsatz digitaler Zwillinge und Agentensysteme werden die Prozesse innerhalb der Elektrolyseanlagen analysiert und verbessert. Diese digitalen Modelle simulieren das Verhalten von Anlagen mit einer Leistungsaufnahme von über 100 MW und bilden das gesamte Spektrum der Wertschöpfungskette ab.
Ein Hauptziel von eModule ist es, einen hersteller- und prozessunabhängigen Standard für die Beschreibung von Wasserelektrolyseuren zu entwickeln. Dieser Standard soll es ermöglichen, mögliche Schwachstellen in großskalierten Anlagen frühzeitig zu erkennen und die Anlagen effizient und ohne unnötige Testphasen in das Energienetz zu integrieren. Das Projekt trägt damit wesentlich zur Optimierung der Produktion von Grünem Wasserstoff bei und unterstützt die Energiewende durch verbesserte Technologien in der Wasserstoffproduktion.
Langtitel: |
Modellierung, Automatisierung, Integration und Optimierung von modular aufgebauten Elektrolyse-Anlagen |
Förderkennzeichen: |
03HY116 |
Gesamtfördersumme: |
ca. 4,8 Mio. Euro |
Partner: |
Technische Universität Dresden, Helmut-Schmidt-Universität / Universität der Bundeswehr Hamburg (HSU), Deutsches Zentrum für Luft- und Raumfahrt e. V., Verband Deutscher Maschinen und Anlagenbau (VDMA), Semodia GmbH |
Projektlaufzeit: |
01.04.2021 – 31.12.2025 |
Kontakt in das Projekt: |
Prof. Dr.-Ing. Leonhard Urbas |
HyLeiT konzentriert sich auf die elektrische Systemtechnik von Elektrolyseanlagen, insbesondere die Stromrichtertechnik zwischen Netz und Elektrolyseur. Ziel ist es, die Kosten der Leistungselektronik zu senken und die Zuverlässigkeit und Netzdienlichkeit der Anlagen zu verbessern.
Nicht nur im Elektrolyseur selbst, sondern auch in angrenzenden Komponenten gibt es Potenziale für eine signifikante Steigerung der Effizienz. Eine wichtige Rolle spielen dabei die Anbindung der Elektrolyseanlage an das Stromnetz sowie die Wandlung der elektrischen Energie zwischen dem Netz und den Elektrolysestacks. HyLeiT beschäftigt sich mit der elektrischen Systemtechnik von Elektrolyseanlagen, insbesondere mit der Stromrichtertechnik als Bindeglied zwischen Netz und Elektrolyseur.
Ziele sind eine deutliche Kostenminderung in der Leistungselektronik, eine verbesserte Gleichstromqualität am Elektrolyseur, welche wiederum die Zuverlässigkeit und Lebensdauer der Elektrolysestacks positiv beeinflusst, und die Berücksichtigung von Netzdienlichkeitsoptionen im Betrieb. Zu diesem Zweck entwickeln die Partner eine speziell angepasste und optimierte Stromrichtertechnik. Hierbei kommen auch Schaltungstopologien mit anwendungsspezifisch optimierten SiC-Leistungshalbleitern zum Einsatz.
Um die Stromrichter im Systemkontext testen und optimieren zu können, werden echtzeitfähige Simulationsmodelle des Stromnetzes sowie der Elektrolyse-Stacks erstellt. Diese Modelle fließen in eine „Power Hardware in the Loop“-Plattform ein, die es ermöglicht, die entwickelten Stromrichterkonzepte unter verschiedenen Netzbedingungen und Stack-Konfigurationen zu testen.
Dabei sind Szenarien für den Betrieb der Anlagen in Netzen mit hohen Anteilen erneuerbarer Energien von großer Bedeutung. Zur Erhöhung der Effizienz und Zuverlässigkeit wird darüber hinaus die elektrische Verbindungstechnik in Elektrolysegleichrichtern optimiert. Dabei stehen insbesondere die thermische Auslegung sowie Untersuchungen zum Kontakt- und Langzeitverhalten der Verbindungselemente im Vordergrund. Begleitet werden die Entwicklungen mit der Untersuchung neuartiger Schutzkonzepte für die elektrische Systemtechnik. Hierzu müssen Fehler zuverlässig erkannt und selbständig geklärt werden, wodurch die Robustheit des Systems steigt.
Langtitel: |
Kostenoptimierte Systemtechnik und Netzintegration von Systemen für die Erzeugung von grünem Wasserstoff |
Förderkennzeichen: |
03HY117A-E |
Gesamtfördersumme: |
ca. 14,1 Mio. Euro |
Partner: |
Fraunhofer-Gesellschaft zur Förderung der angewandten Forschung e. V., SMA Solar Technology AG, Infineon Technologies AG, Hochschule Bonn-Rhein-Sieg, Technische Universität Dresden |
Projektlaufzeit: |
01.04.2021 – 30.09.2025 |
Kontakt in das Projekt: |
Dr.-Ing. Philipp Strauß |
FluCoM untersucht und entwickelt Methoden zur Überwachung und Aufreinigung des Prozesswassers in Elektrolyseuren. Ziel ist es, die Qualität des Prozesswassers sicherzustellen, um eine zuverlässige und effiziente Wasserstoffproduktion zu gewährleisten.
Das Projekt FluCoM untersucht die Einflüsse unterschiedlicher Wasserqualitäten auf Elektrolyseure. Durch die ständige Zirkulation des Wassers innerhalb der Anlage kann es zu Verunreinigungen durch Metallionen und andere Substanzen wie Silizium kommen, die die Leistung des Elektrolyseurs beeinträchtigen. Ziel des Projektes ist es, durch innovative Überwachungsmethoden diese Verunreinigungen präzise zu erfassen und die Prozesswasseraufbereitung zu optimieren. Damit soll die Langlebigkeit und Zuverlässigkeit der Wasserstoffproduktion verbessert werden. Ein wichtiges Projektziel liegt in der Aufklärung von Störstoffen und der Definition von Mindestqualitäten, die für einen sicheren Betrieb eines Elektrolyseurs erforderlich sind.
Langtitel: |
Fluid Condition Monitoring |
Förderkennzeichen: |
03HY118A-B |
Gesamtfördersumme: |
ca. 700.000 Euro, davon ca. 420.000 Euro durch das BMBF |
Partner: |
TEC4FUELS GmbH, DECHEMA-Forschungsinstitut |
Projektlaufzeit: |
01.04.2021 – 31.03.2025 (teilweise verlängert bis 30.09.2025) |
Kontakt in das Projekt: |
Klaus Lucka |
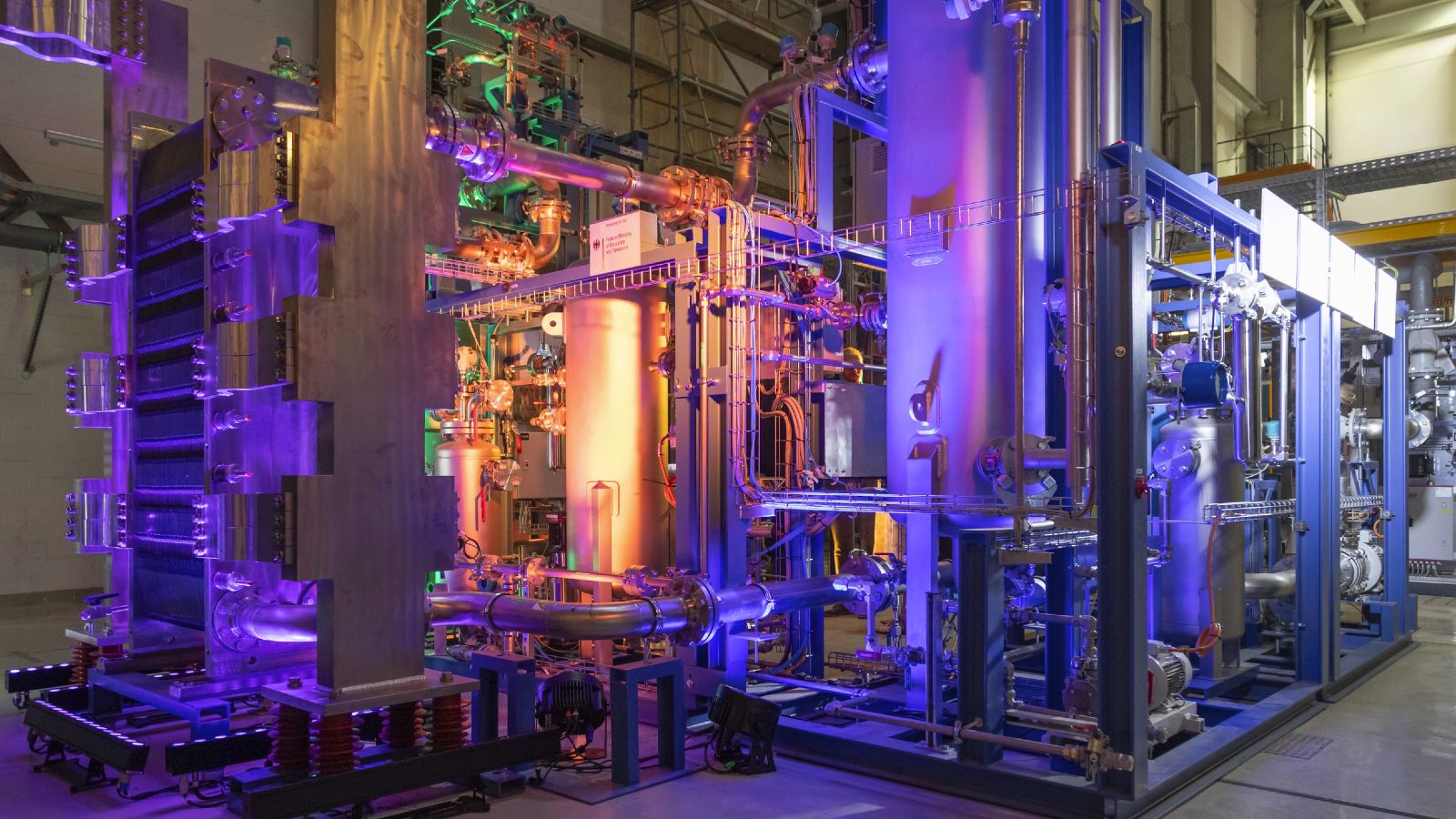
Plattform-Projekt: Technologieplattform Elektrolyse
Über die Technologieplattform Elektrolyse stehen Wissenschaft und Industrie im steten Austausch miteinander, so dass die Partner Wissenslücken schließen und bei Forschungsthemen die spätere Anwendbarkeit von Anfang an mitdenken können. Auch übergreifende nicht-technische Themen, z. B. Weiterbildungsmaßnahmen oder die Vereinfachung von Genehmigungsverfahren, werden hier bearbeitet.
Die Technologieplattform Elektrolyse, kurz TPE, gewährleistet den Informationsaustausch zwischen den Projekten von H2Giga. Der Verbund adressiert zudem nichttechnische Innovationshürden und erarbeitet eine Roadmap Elektrolyse.
Um den kontinuierlichen Informationsfluss zu gewährleisten, tauschen sich die Partner in themenspezifischen Arbeitsgruppen aus. Auch die Querschnitts-Projekte des Innovationspools und die industriegeführten Verbünde vernetzen sich in regelmäßigen Treffen, um den Stand in Forschung und Industrie abzugleichen. So können sie Synergien optimal nutzen.
TPE übernimmt auch übergeordnete inhaltliche Aufgaben. So erarbeitet sie eine technologische Roadmap zur Elektrolyse, die den Stand des Scale-ups für verschiedene Elektrolysetechnologien zusammenfasst, offene technische Fragen und Forschungsbedarfe listet und Pfade für weitere Arbeiten in Richtung Gigawatt-Maßstab vorschlägt. Auch ein Weiterbildungsprogramm mit Grund- und Praxiskursen zu Prozess- und Materialfragen sowie Sicherheit und Betrieb entwickelt TPE.
Ein weiteres Ziel der Plattform ist es, Innovationshürden abzubauen. Dabei konzentrieren sich die Partner auf beschleunigte Zertifizierungs- und Genehmigungsverfahren für verschiedene Anlagenkonzepte sowohl in Deutschland als auch in möglichen Exportländern. Auch die Bereiche Testung und Normung von Elektrolyseuren, insbesondere Prüfverfahren, stehen im Fokus.
Langtitel: |
Technologieplattform Elektrolyse |
Förderkennzeichen: |
03HY101A-E |
Gesamtfördersumme: |
ca. 7,8 Mio. Euro |
Partner: |
DECHEMA e. V., DECHEMA Forschungsinstitut, DBI Gastechnologisches Institut, TÜV Rheinland Industrie Services, keep it green GmbH |
Projektlaufzeit: |
01.04.2021 – 31.12.2025 |
Kontakt in das Projekt: |
Dr. Isabel Kundler |